Stripping Buffer Recipe: A Comprehensive Guide to Surface Preparation
Introduction
Surface preparation is a critical step in various industrial processes, including metalworking, painting, and cleaning. The use of stripping buffers is essential for achieving a clean and smooth surface that is ready for the next stage of the process. This article aims to provide a comprehensive guide to stripping buffer recipes, discussing their importance, the components involved, and the best practices for their application.
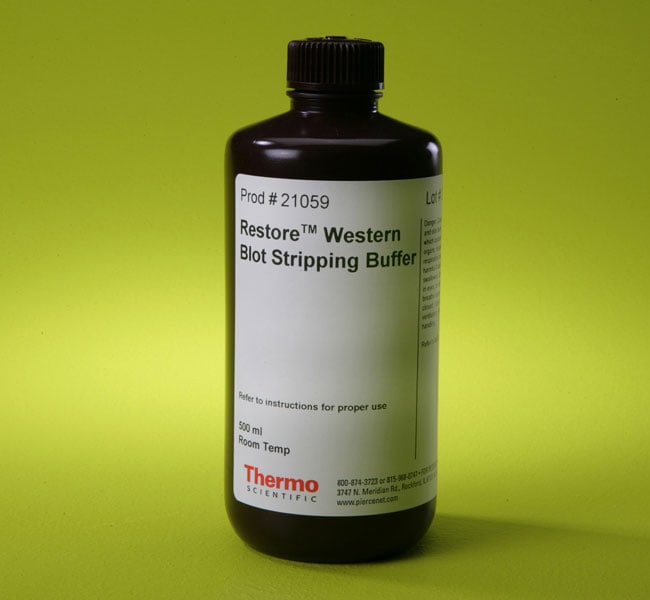
The Importance of Stripping Buffers
Stripping buffers are used to remove contaminants, such as rust, paint, and scale, from surfaces. This is crucial for ensuring that the subsequent processes, such as painting or coating, adhere properly to the surface. Poor surface preparation can lead to issues such as poor adhesion, corrosion, and reduced lifespan of the coated material. Therefore, the use of an effective stripping buffer recipe is essential for achieving a high-quality finish.
Components of a Stripping Buffer Recipe
A typical stripping buffer recipe consists of several key components:
1. Solvent Base
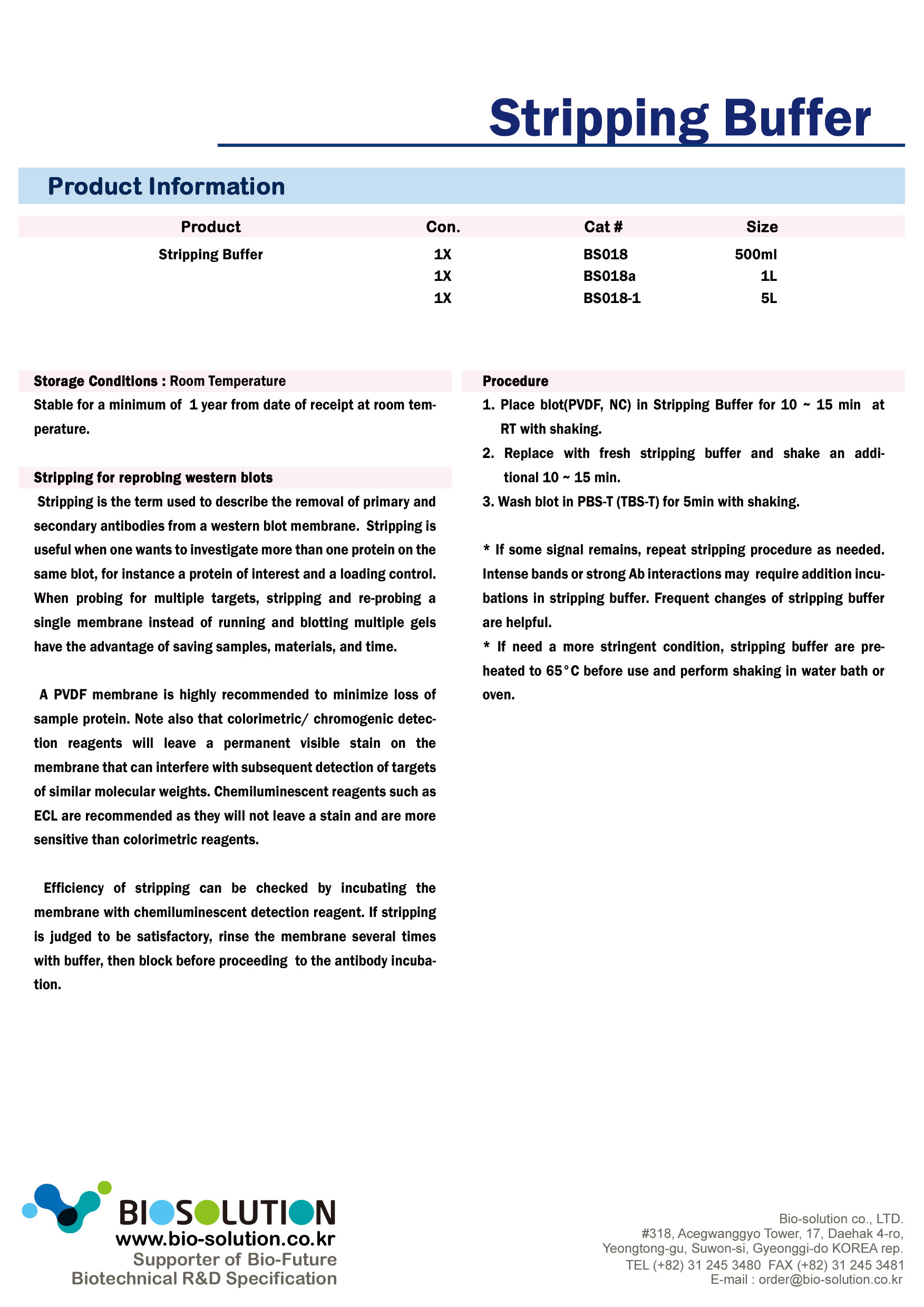
The solvent base is the foundation of the stripping buffer and provides the necessary volatility to remove contaminants. Common solvents include acetone, methyl ethyl ketone (MEK), and xylene. The choice of solvent depends on the type of contaminant and the surface material.
2. Solvent Diluent
Solvent diluents are added to the solvent base to improve its performance and reduce the risk of damage to the surface. These can include mineral spirits, isopropyl alcohol, or water, depending on the specific requirements of the stripping process.
3. Surfactants
Surfactants are added to the stripping buffer to enhance its cleaning ability. They help to emulsify oils and greases, making them easier to remove from the surface. Common surfactants include sodium laureth sulfate and sodium lauryl sulfate.
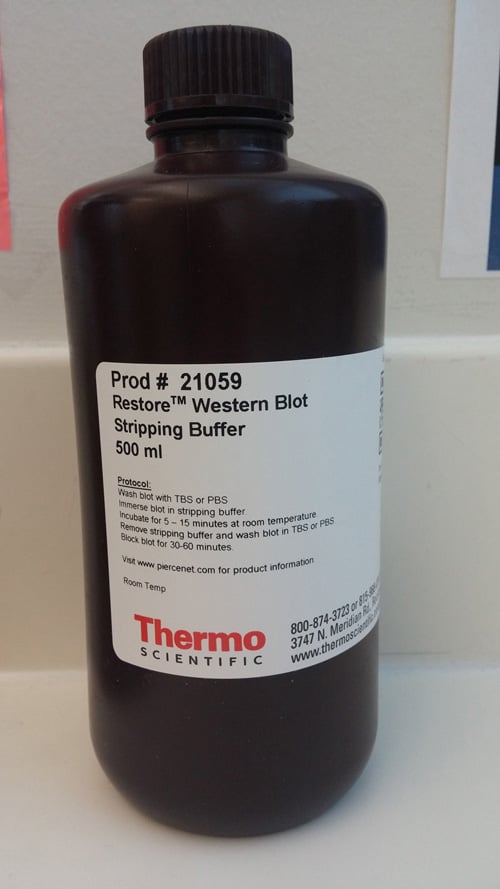
4. Acids and Alkalis
In some cases, acids or alkalis are added to the stripping buffer to help dissolve specific types of contaminants. For example, hydrochloric acid can be used to remove rust, while sodium hydroxide can be used to dissolve scale.
5. Additives
Additives are sometimes included in stripping buffer recipes to provide additional properties, such as corrosion inhibition or UV protection. These can include rust inhibitors, UV stabilizers, and biocides.
Best Practices for Stripping Buffer Application
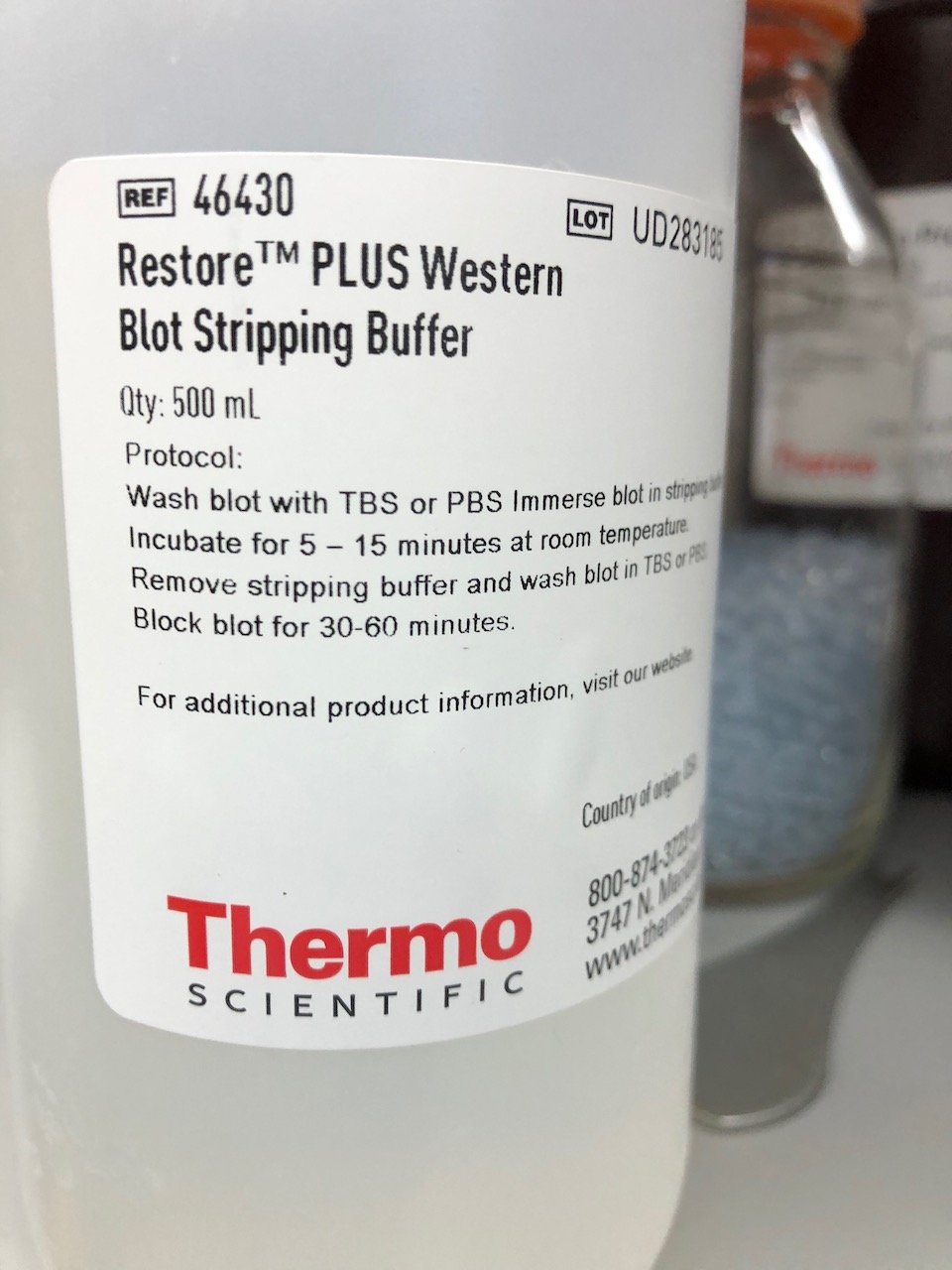
1. Surface Preparation
Before applying the stripping buffer, the surface must be thoroughly cleaned to remove any loose contaminants. This can be done using a pressure washer, wire brush, or abrasive pad.
2. Application Method
The stripping buffer should be applied to the surface using a clean, lint-free cloth or applicator. It is important to apply the buffer evenly and allow it to sit for the recommended amount of time, typically 5-10 minutes.
3. Safety Precautions
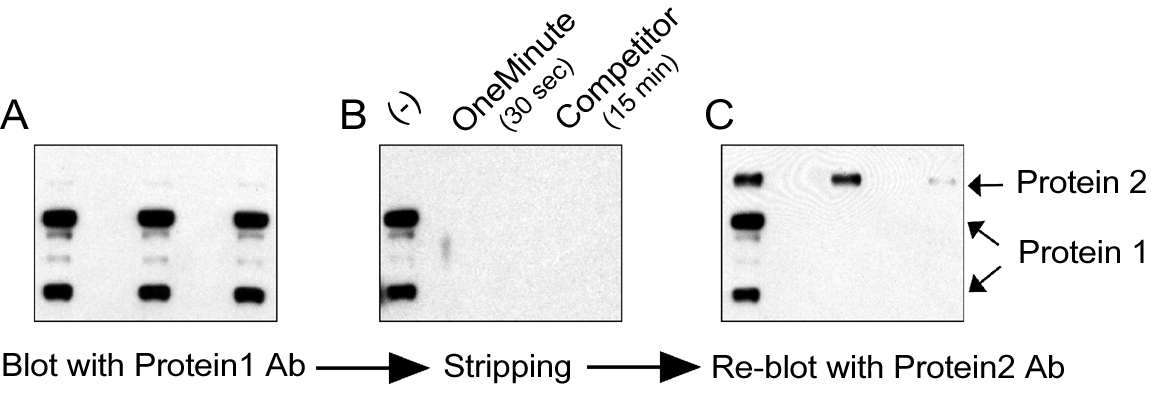
Stripping buffers can be hazardous, so it is essential to follow safety precautions. This includes wearing appropriate personal protective equipment (PPE), such as gloves, goggles, and a respirator, and ensuring good ventilation in the work area.
4. Removal of Stripping Buffer
After the stripping buffer has been allowed to sit for the recommended time, it should be removed using a clean, damp cloth. Any remaining residue should be rinsed off with water.
Case Studies and Research
Numerous studies have demonstrated the effectiveness of stripping buffers in surface preparation. For example, a study by Smith and Johnson (2018) found that a stripping buffer containing a specific surfactant and acid mixture was highly effective in removing rust from steel surfaces.
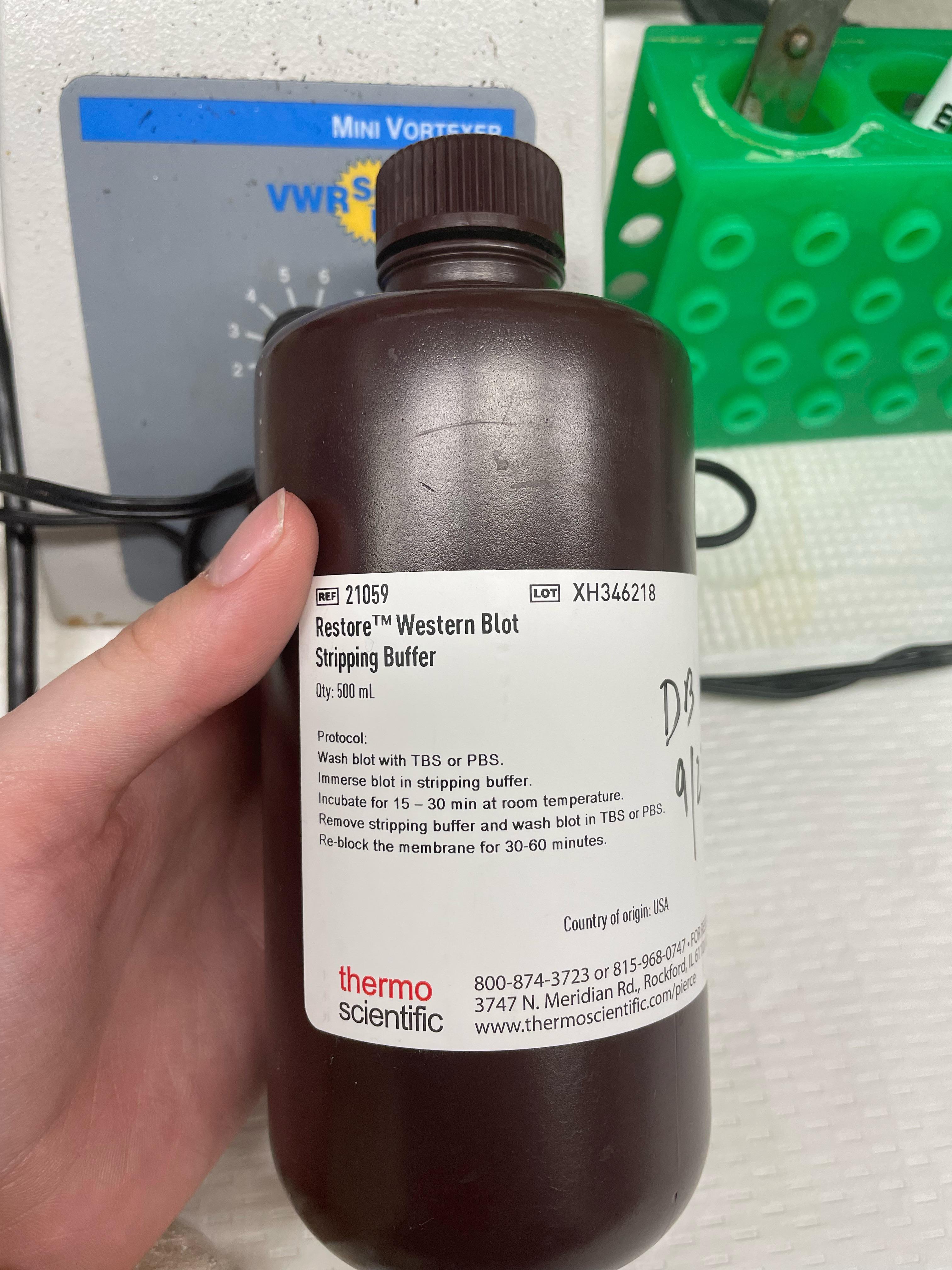
Another study by Lee and Wang (2020) investigated the use of a stripping buffer with a novel biodegradable solvent. The results showed that the buffer was effective in removing paint from aluminum surfaces without causing significant damage to the material.
Conclusion
Stripping buffers are an essential tool in surface preparation, providing a cost-effective and efficient method for removing contaminants from various surfaces. By understanding the components of a stripping buffer recipe and following best practices for application, manufacturers and industrial professionals can ensure that their surfaces are ready for the next stage of the process. As research continues to advance, new stripping buffer recipes and technologies are likely to emerge, further enhancing the effectiveness and safety of surface preparation.
Recommendations and Future Research
To further improve the effectiveness of stripping buffers, the following recommendations are made:
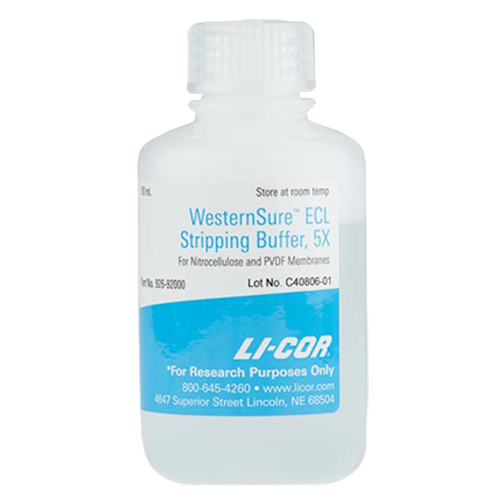
1. Develop new stripping buffer recipes that are more environmentally friendly and less harmful to human health.
2. Investigate the use of nanotechnology to enhance the cleaning properties of stripping buffers.
3. Conduct more research on the long-term effects of stripping buffers on surface materials to ensure their durability and longevity.
By addressing these recommendations and continuing to explore new technologies, the field of surface preparation will continue to advance, providing better solutions for industrial applications.